What Therser Wellman Offer
Extensive Alloy Expertise: Therser Wellman boasts a team of highly skilled engineers and technicians with years of experience in alloy fabrication. We understand the unique properties and characteristics of various alloys, enabling us to deliver fantastic results.
Customized Solutions: We take pride in tailoring our services to your specific requirements. Whether you need precision components, intricate designs, or large-scale fabrication, our team can create the perfect solution for your project.
Cutting-edge Technology: Our advanced fabrication facilities are equipped with state-of-the-art machinery and technology. This allows us to leverage the latest innovations to achieve high-quality results efficiently and cost-effectively.
High-Quality Materials: We source premium-grade alloys from trusted suppliers, ensuring that your fabricated products possess superior durability, strength, and resistance to various environmental factors.
Prototyping and Design Support: Our team can assist you throughout the product development process, providing valuable insights and collaborating on the design to optimize performance and manufacturability.
Rapid Turnaround: Time is of the essence in the fast-paced business world. Therser Wellman is committed to delivering projects on schedule without compromising on quality, helping you stay ahead of the competition.
Quality Assurance: We maintain strict quality control measures at every stage of fabrication. Your satisfaction is our priority, and we ensure that every component meets the highest standards before leaving our facility.
Cost-Effective Solutions: Our streamlined processes and efficient use of resources enable us to offer competitive pricing without compromising on quality or precision.
Versatile Applications: Therser Wellman's alloy fabrication solutions find application in a wide range of industries, including aerospace, automotive, energy, and manufacturing, among others.
Customer-centric Approach: Our dedicated team is always ready to listen to your needs, address your concerns, and provide exceptional customer service throughout your project journey.
What Is Alloy Fabrication
Alloy fabrication is the process of shaping, cutting, and assembling components made from metal alloys. This can include techniques such as casting, welding, machining, and forming. The goal of alloy fabrication is to create a finished product that meets specific design specifications and tolerances. Common products created through alloy fabrication include structural components, machinery and equipment, and aerospace and automotive parts.
There are several steps involved in the process of alloy fabrication:
Design and planning: The first step is to create detailed plans and blueprints for the finished product. This includes determining the materials to be used, the specific alloy, and the overall dimensions and shape of the product.
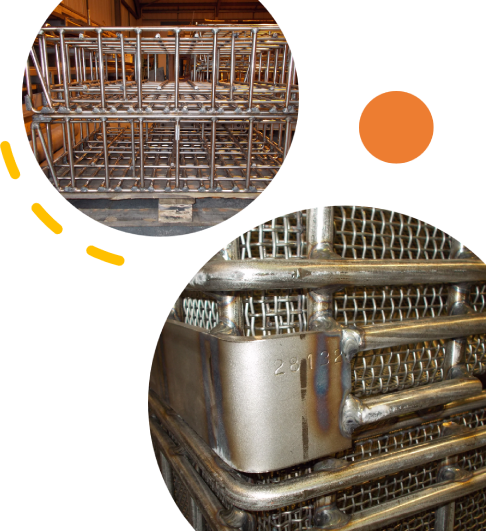
Material preparation: The materials, usually in the form of metal alloy sheets or rods, are then prepared for fabrication. This may involve cutting the materials to the correct size and shape.
Forming: The materials are then formed into the desired shape using techniques such as stamping, casting, or rolling.
Machining: The formed parts are then machined to their final shape using techniques such as drilling, turning, milling, or grinding.
Assembly: The parts are then assembled together using techniques such as welding, riveting, or bolting.
Finishing: The final product is then finished to the desired surface finish. This can include cleaning, polishing, painting or other surface treatment.
Inspection: Quality inspection is performed on final product, checking if the product has the right dimension and mechanical properties.
There are many different types of metal alloys that can be used in alloy fabrication, depending on the specific properties and characteristics required for the finished product. Some common metals and alloys used in alloy fabrication include:
Aluminum: Lightweight, corrosion-resistant, and good for high-temperature applications.
Steel: Strong, durable, and widely used in construction and machinery.
Copper: Good electrical and thermal conductivity, corrosion-resistant, and used in electrical components and piping.
Titanium: Strong, corrosion-resistant, and biocompatible, used in aerospace and medical applications.
Nickel: Good corrosion resistance and strength at high temperatures, used in power generation and chemical processing.
Magnesium: Lightweight, good for high-temperature applications and shock absorption.
Zinc: Good corrosion resistance, used in galvanizing and electroplating.
Gold: Good electrical conductivity, used in electronics and jewelry.
Silver: Good electrical conductivity and reflectivity, used in electronics and mirrors
Tungsten : High density, high melting point, and good resistance to wear and tear..
Alloy fabrication involves various processes to create, shape, and manipulate alloys. Some of the different processes in alloy fabrication include:
Melting: The first step in alloy fabrication is usually melting the constituent metals or elements together. This can be done using methods like electric arc furnaces, induction melting, or gas-fired furnaces. Melting ensures the homogeneity of the alloy by allowing the elements to mix thoroughly.
Casting: Once the alloy is melted and properly mixed, it can be cast into specific shapes using molds. Casting processes include sand casting, investment casting, die casting, and continuous casting, depending on the complexity and requirements of the final product.
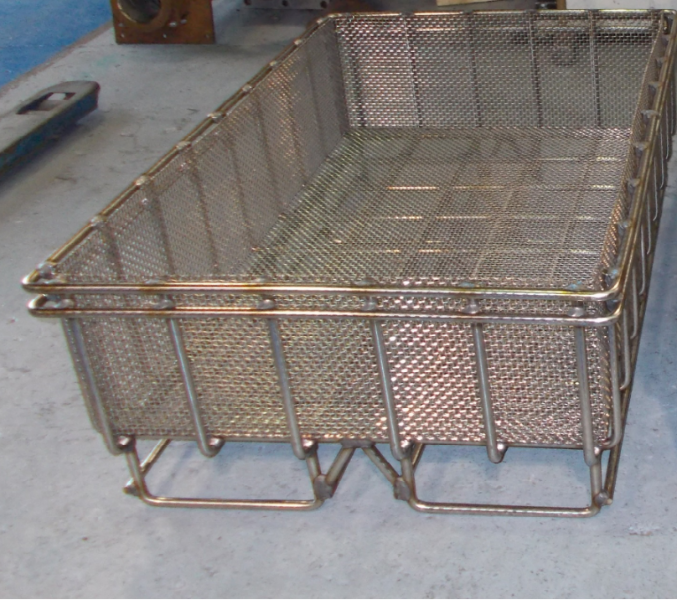
Forging: Forging involves shaping the alloy by applying compressive forces using hammers, presses, or other machinery. It helps to improve the mechanical properties of the alloy, such as strength and durability, by aligning the crystal structure and reducing porosity.
Rolling: Rolling is a process where the alloy is passed through rollers to reduce its thickness or shape it into sheets, plates, or other forms. This process can improve the mechanical properties and grain structure of the alloy.
Extrusion: Extrusion is used to create complex shapes by forcing the alloy through a die with a specific cross-sectional profile. It is commonly used in manufacturing tubes, rods, and profiles.
Heat treatment: Heat treatment is an essential process in alloy fabrication. It involves controlled heating and cooling of the alloy to alter its microstructure and properties. Different heat treatment methods, such as annealing, quenching, tempering, and aging, can be used to achieve specific hardness, strength, or other desired characteristics.
Welding and Joining: Joining different alloy components together is often necessary to create complex structures. Welding, brazing, soldering, and adhesive bonding are common methods used for this purpose.
Machining: After the alloy is fabricated into its final form, machining processes like cutting, drilling, milling, and turning may be employed to achieve precise dimensions or add further details.
Surface treatment: Surface treatments like coating, plating, or passivation can be applied to enhance the alloy's properties, such as corrosion resistance or appearance.
In alloy fabrication, heat treatment is a crucial process used to alter the microstructure of the alloy and, consequently, its mechanical properties. There are several different heat treatment methods commonly employed, each serving specific purposes. Some of the key heat treatments in alloy fabrication include:
Annealing: Annealing involves heating the alloy to a specific temperature and holding it there for a period of time, followed by slow cooling. This process is used to soften the alloy, relieve internal stresses, and refine the grain structure. Annealing improves the machinability and ductility of the alloy, making it easier to work with and less prone to cracking during subsequent processes.
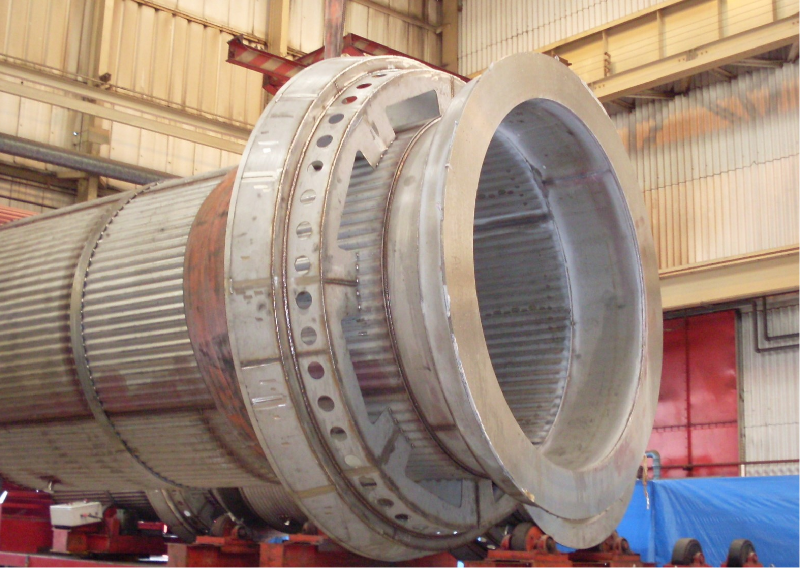
Quenching: Quenching is a rapid cooling process that involves immersing the heated alloy into a quenching medium, such as water, oil, or polymer. This rapid cooling "freezes" the microstructure, resulting in increased hardness and strength. Quenching is used to achieve materials with high hardness, but it can also make the alloy more brittle, so a subsequent tempering process is often required.
Tempering: Tempering follows quenching and involves reheating the quenched alloy to a specific temperature and holding it there for a predetermined time. This controlled reheating reduces the brittleness caused by quenching and imparts toughness and ductility to the alloy. The resulting material is still strong but less likely to fracture under stress.
Normalizing: Normalizing is a heat treatment process similar to annealing, but it involves cooling the alloy in still air rather than a furnace. Normalizing is used to refine the grain structure and improve the uniformity of the alloy's mechanical properties. It provides a balance of strength and ductility.
Precipitation Hardening (Age Hardening): Precipitation hardening is a two-step process used to strengthen certain alloys, particularly those containing elements like aluminum, copper, or titanium. It involves solution treatment (heating the alloy to dissolve the precipitates) and then aging (reheating at a lower temperature to allow new precipitates to form). The resulting alloy is significantly stronger and can maintain this strength at elevated temperatures.
Case Hardening: Case hardening is a surface heat treatment used to improve the wear resistance of alloys. It involves adding carbon or nitrogen to the surface layer of the alloy by heating it in a carbon- or nitrogen-rich environment. The core remains relatively soft and tough, while the surface becomes hard and wear-resistant.
Stress Relieving: Stress relieving is a low-temperature heat treatment used to remove residual stresses in the alloy after fabrication or welding. The alloy is heated to a specific temperature and then allowed to cool slowly, which reduces internal stresses without significantly altering the material's properties.
Each of these heat treatments offers unique advantages and is chosen based on the specific alloy composition and desired properties for the final application. Skilled metallurgists and engineers carefully design and control the heat treatment processes to achieve the desired characteristics in the fabricated alloy.
Typical metals Therser Wellman Fabrication work with:
Nickel Alloy
- 600
- 601
- 625,
- 800HT
Hastelloy
- C22
- C276
Duplex
- Super Duplex
Stainless steel
- 304L
- 310,
- 316L
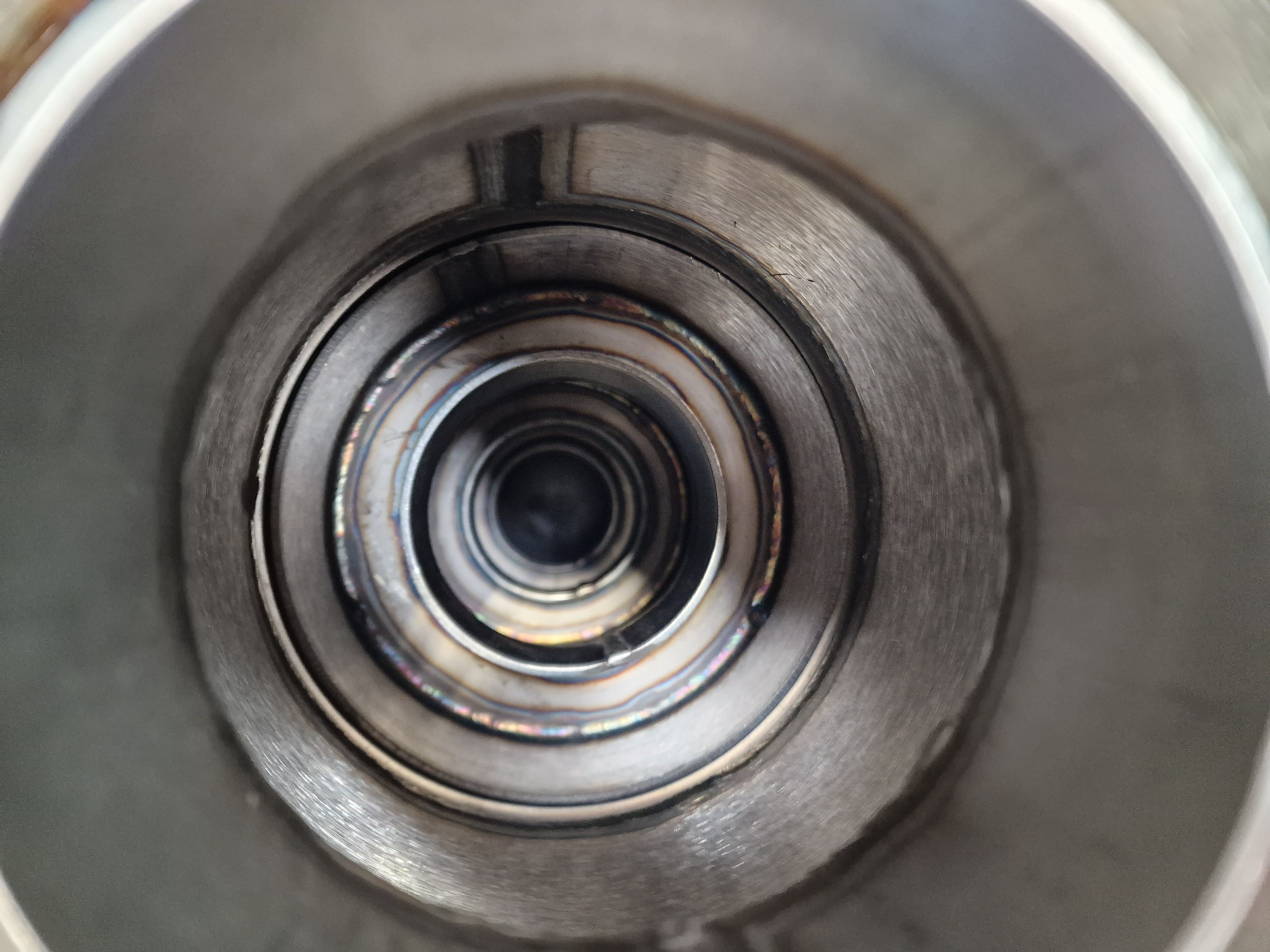
ALLOY FABRICATION
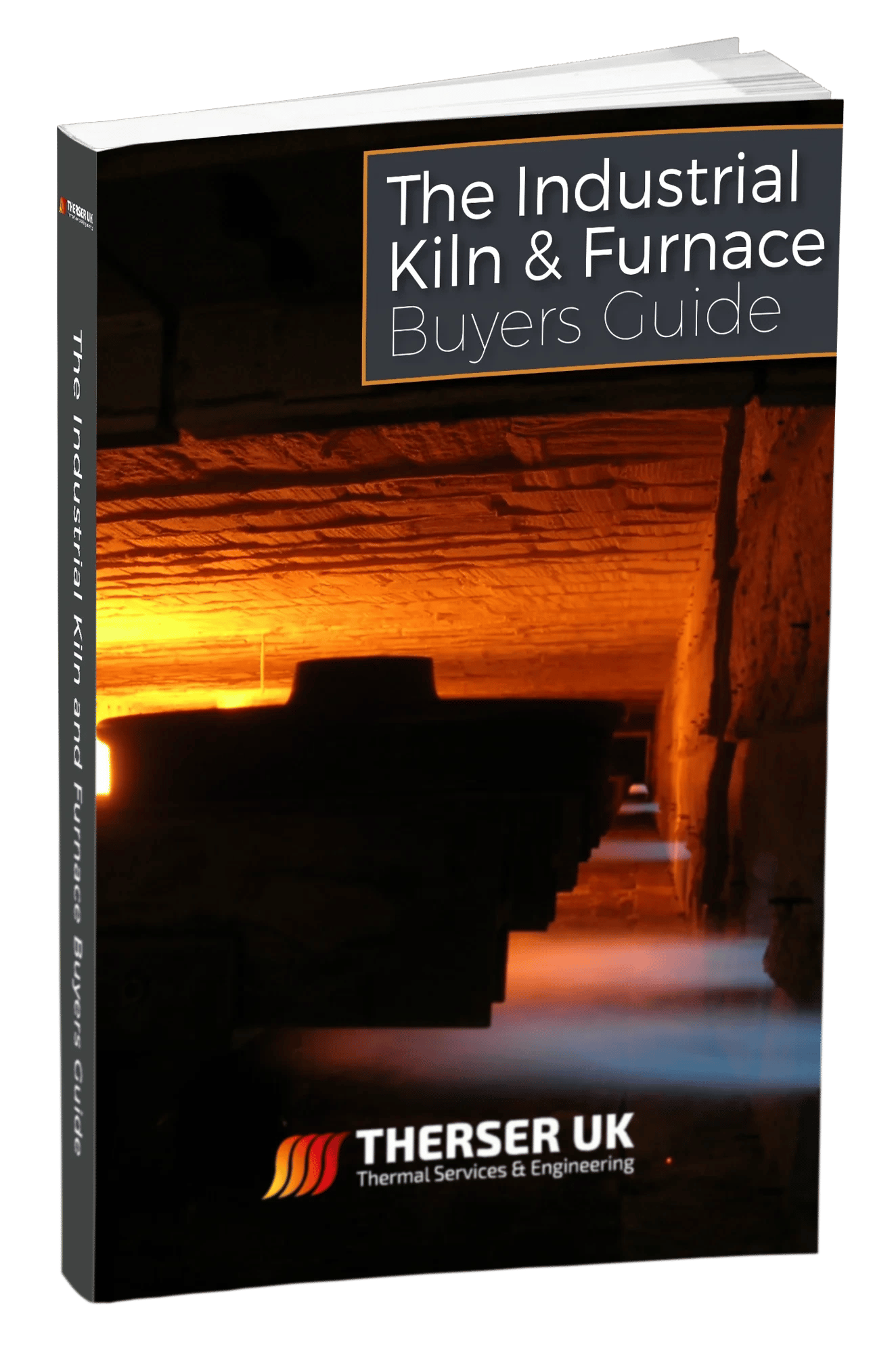
DOWNLOAD THE INDUSTRIAL KILN & FURNACE BUYERS GUIDE
If you need, or may need in the future, to invest in an industrial kiln, furnace or oven, then get a copy of this FREE guide today.
Discover:
- How to choose the right type of kiln or furnace
- How to avoid the most common mistakes with industrial kilns and furnaces
- How to ensure maximum fuel efficiency
So confirm your correct email address using the form provided and your copy will be in your inbox within seconds!
OUR CERTIFICATIONS
REVIEWS
TALK TO US TODAY
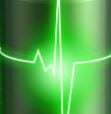
