Hydrogen Kiln Technology
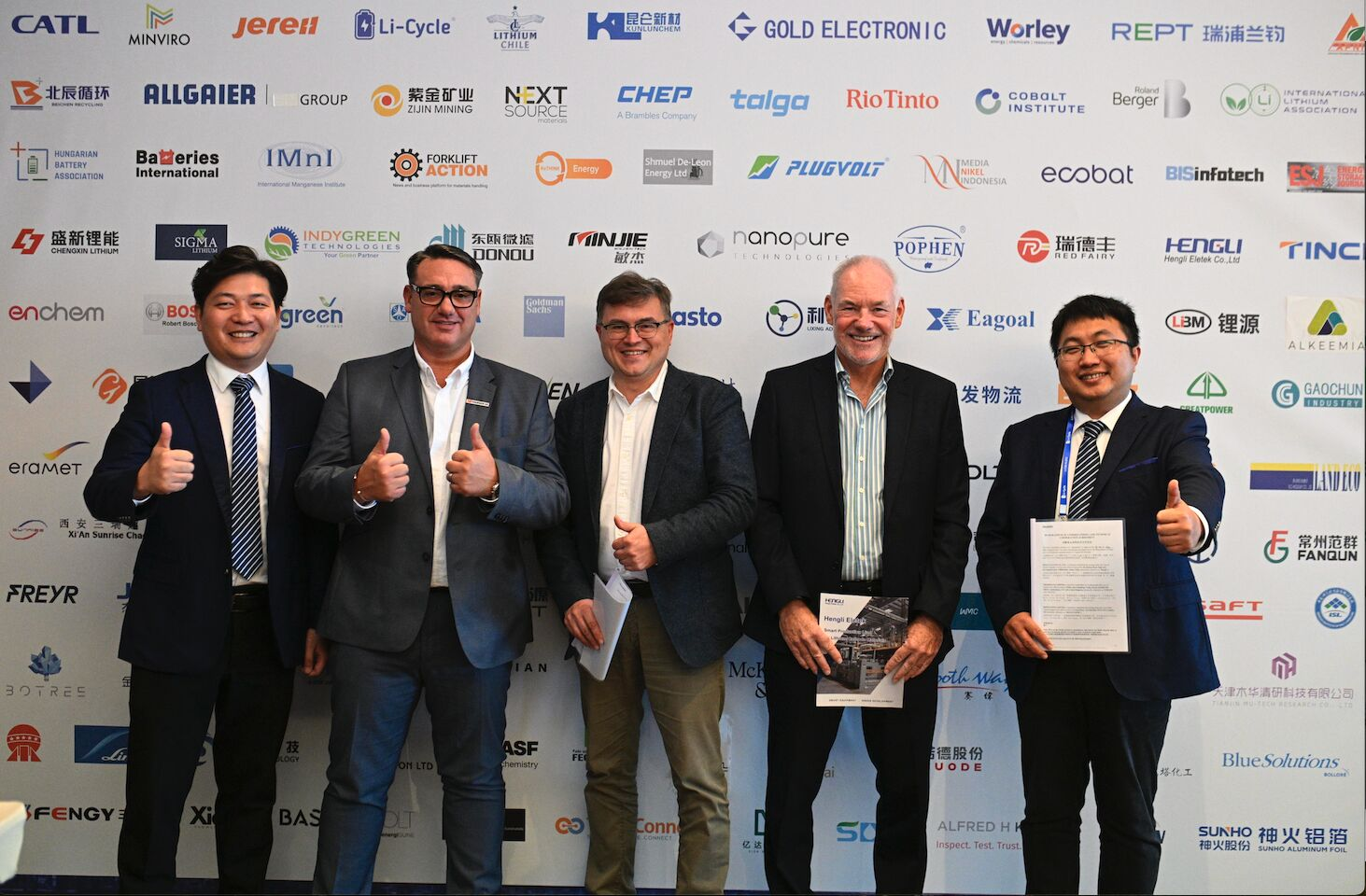
MOU Memorandum Of Understanding, Signed 2023 between Therser UK, Hengli and Honeystone
KILNS
Hydrogen, denoted chemically as H₂, presents a viable alternative fuel source for kilns, substituting traditional fuels like natural gas, primarily composed of methane (CH₄), or other hydrocarbon-based fuels. The application of hydrogen in thermal processes necessitates stringent adherence to safety protocols due to its inherent properties. Hydrogen's high flammability and potential for explosive reactions, particularly when mixed with oxygen (O₂) in the air, demand careful monitoring and management.
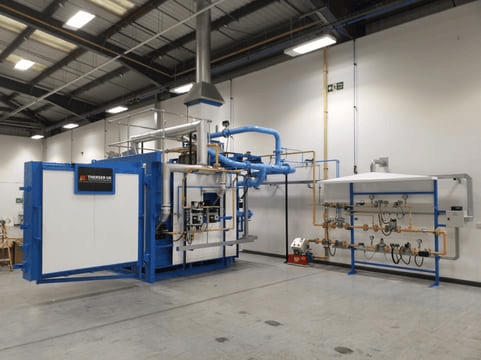
This gas has a wide flammability range between 4% and 75% in air, necessitating precise control over its concentration to prevent combustion-related hazards. Furthermore, the low ignition energy of hydrogen compared to other fuels like methane increases the risk of accidental ignition.
From an engineering perspective, the kiln and associated fuel delivery systems must be specifically designed or adapted to handle hydrogen's unique properties. This includes considerations for hydrogen's low molecular weight and high diffusivity, which can lead to rapid dispersion in the air and potential leakage through smaller openings than other gases. Materials selection for the kiln and fuel system components must also account for hydrogen embrittlement, where certain metals become brittle and crack in the presence of hydrogen.
Ensuring a robust and leak-proof fuel system, along with reliable sensors and controls to monitor hydrogen concentration, pressure, and flow rates, is crucial for the safe and efficient utilization of hydrogen as a kiln fuel.
TEST KILN
Hydrogen stands as a transformative fuel for kiln operations, providing a flexible alternative to conventional fuels such as natural gas, which is principally composed of methane (CH₄). Its employment in kiln systems presents an opportunity for heightened efficiency and a marked reduction in environmental impact. Nonetheless, the utilization of hydrogen necessitates rigorous safety protocols due to its extensive flammability range, necessitating precise control over ambient hydrogen concentrations.
The engineering of kiln and fuel infrastructure demands bespoke adaptations to accommodate the characteristics of hydrogen. This includes designing for its low density and high energy content, ensuring robust containment to prevent leaks, and implementing advanced monitoring systems for detecting hydrogen levels.
Achieving the full potential of hydrogen in kiln technology requires a delicate equilibrium between ensuring operational safety and optimizing performance. Thorough planning, design, and the implementation of sophisticated control systems are crucial in realizing the benefits of hydrogen as a kiln fuel, enabling a sustainable and efficient thermal process within the industry.
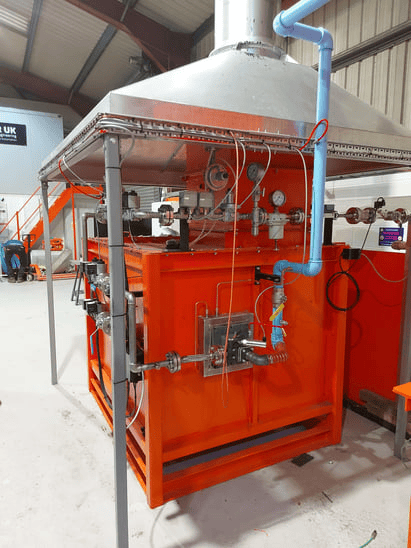
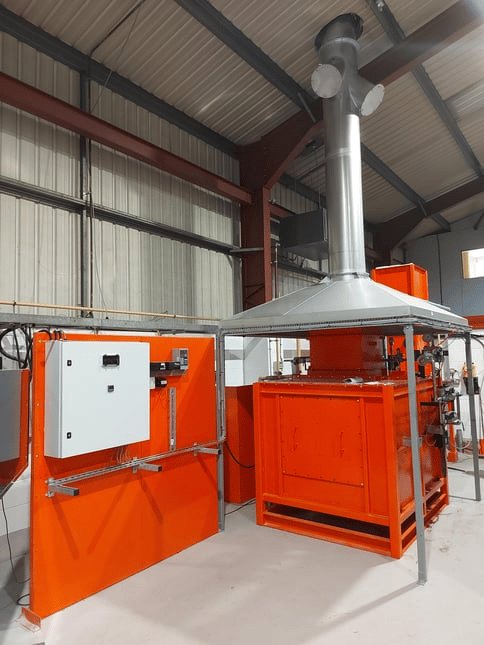
R & D
At the Therser UK Research and Development facility in Burslem, our kiln is at the vanguard of thermal processing innovation, utilizing a combustion system capable of operating with a hydrogen (H₂) fuel blend ranging from 30 to 100 percent. This strategic advancement capitalizes on hydrogen's high diffusivity and low ignition energy to enhance thermal efficiency while significantly reducing the environmental impact. Therser UK's pioneering approach to kiln design represents a paradigm shift from reliance on traditional fuels such as natural gas, typically composed of alkanes (C_nH_(2n+2)), to cleaner alternatives. The use of hydrogen as a fuel results in the production of water vapor (H₂O) instead of carbon dioxide (CO₂), thereby dramatically lowering greenhouse gas emissions.
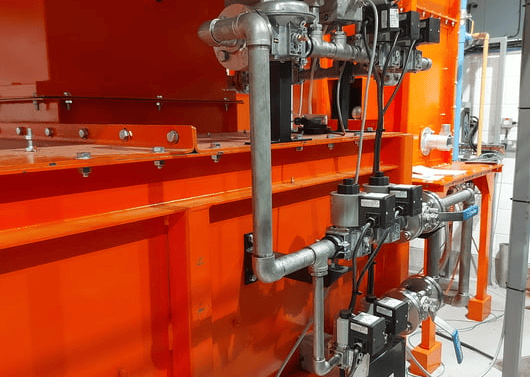
Addressing the challenges associated with hydrogen, such as its propensity for embrittlement and its broad flammability range, Therser UK's Burslem facility features a kiln constructed with advanced materials and engineered to ensure safe hydrogen integration.
Therser UK's leadership in the deployment of hydrogen-fueled kiln technology is a testament to the company's commitment to sustainable manufacturing. This initiative not only supports the decarbonization efforts within the ceramics industry but also aligns with global sustainability objectives, setting a benchmark for the adoption of clean energy in industrial high-temperature processes.
Different ways to create hydrogen
Green hydrogen represents a sustainable energy source, generated by electrolyzing water into hydrogen (H₂) and oxygen (O₂) using electricity derived from renewable resources. This production method stands in stark contrast to both grey and blue hydrogen production pathways.
Grey hydrogen iGrey hydrogens primarily produced through steam methane reforming (SMR), where methane (CH₄) reacts with steam, yielding carbon dioxide (CO₂) – a principal contributor to climate change – and hydrogen (H₂). This process, sometimes utilizing coal, results in even higher CO₂ emissions, leading to its alternative monikers, brown or black hydrogen. Currently produced at an industrial scale, grey hydrogen's emissions are significant, rivaling the combined outputs of the UK and Indonesia and offering no benefit to the energy transition.
Blue hydrogen, while following the same SMR process as grey hydrogen, incorporates carbon capture and storage (CCS) technologies to sequester the resultant CO₂. This method does not represent a single solution but rather a spectrum of possibilities, as capturing 100% of CO₂ is not currently feasible and the long-term efficacy of storage methods varies. The primary advantage of blue hydrogen is its potential to reduce the climate impact of hydrogen production substantially.
Turquoise hydrogen emerging on the horizon of hydrogen production technologies. This involves methane pyrolysis, a process that can potentially capture 90-95% of CO₂ in a solid form, offering a more effective long-term storage solution. Although still in the experimental phase, Turquoise hydrogen holds the promise of a superior alternative within the "hydrogen color spectrum."
Meanwhile, green hydrogen is advancing rapidly, scaling up through the adoption of two essential technologies: renewable power sources, especially solar photovoltaics (PV) and wind, and water electrolysis. This progress underscores the potential of green hydrogen as a cornerstone of a cleaner, renewable energy landscape.
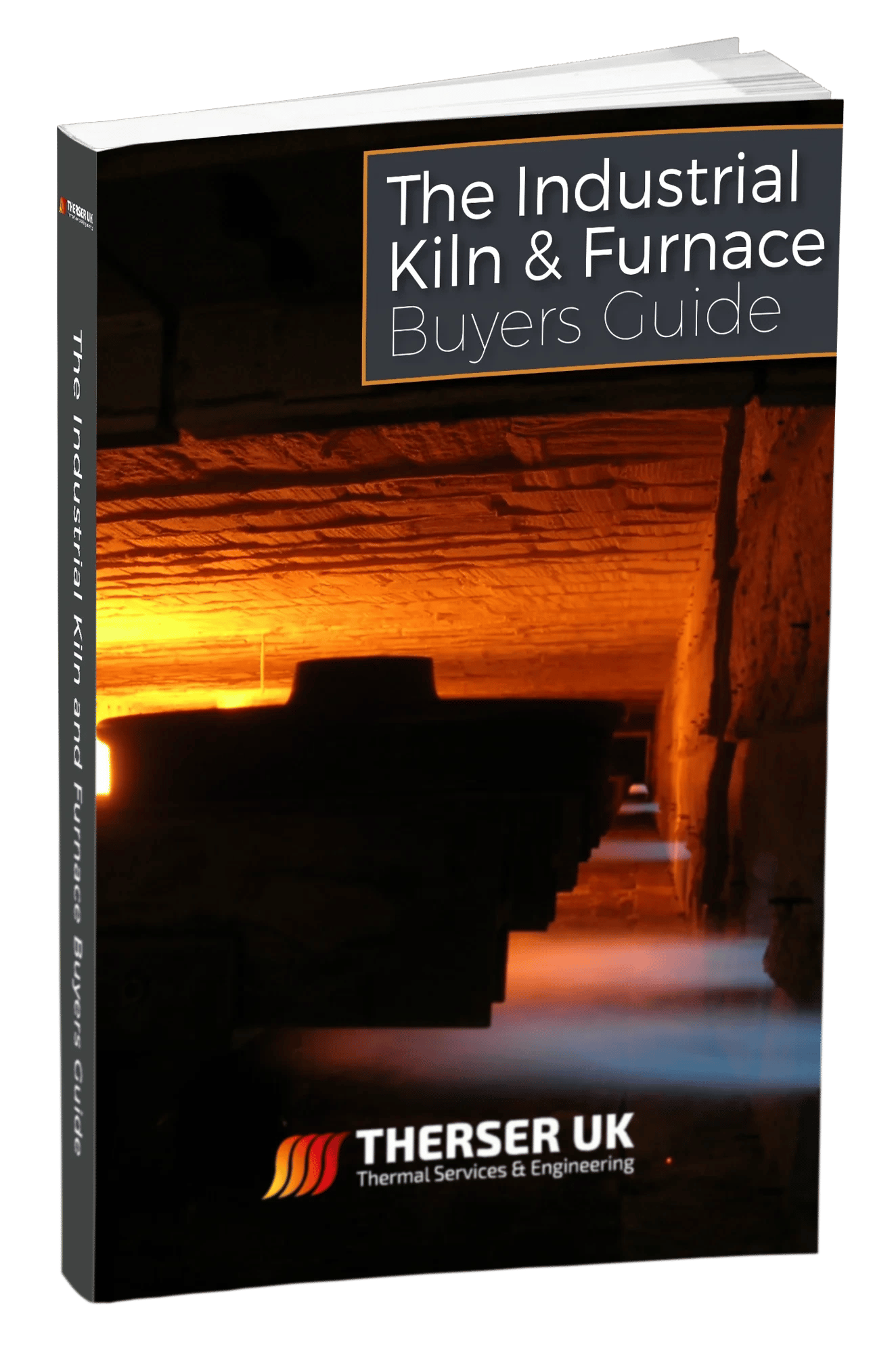
DOWNLOAD THE INDUSTRIAL KILN & FURNACE BUYERS GUIDE
If you need, or may need in the future, to invest in an industrial kiln, furnace or oven, then get a copy of this FREE guide today.
Discover:
- How to choose the right type of kiln or furnace
- How to avoid the most common mistakes with industrial kilns and furnaces
- How to ensure maximum fuel efficiency
So confirm your correct email address using the form provided and your copy will be in your inbox within seconds!
OUR CERTIFICATIONS
REVIEWS
TALK TO US TODAY
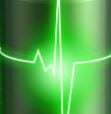
