Calcination of Battery Materials
Calcination of Battery Materials
Battery Materials
Lithium-ion batteries stand at the forefront of modern energy storage solutions, heralding a new era in both mobility and portable electronic devices. These batteries are not just another product on the market; they are a pivotal innovation driving the future of Electric Vehicles (EVs), smartphones, laptops, and a myriad of other gadgets that define our daily lives. What sets lithium-ion batteries apart is their remarkable combination of lightness, high energy density, and the strategic incorporation of metals and their chemical compounds, such as lithium cobalt oxide (LiCoO₂), lithium nickel manganese cobalt oxide (LiNiMnCoO₂ or NMC), lithium iron phosphate (LiFePO₄), and lithium nickel cobalt aluminum oxide (LiNiCoAlO₂ or NCA). These compounds play crucial roles in enhancing battery performance, resulting in longer usage times and significantly reduced weight compared to their predecessors.
This unique blend of features, including the precise engineering of chemical elements and compounds, makes lithium-ion batteries an indispensable asset in today's fast-paced world, where efficiency and sustainability are paramount. Whether it's powering an electric car to achieve unprecedented ranges on a single charge or ensuring that a smartphone can last through the busiest of days, lithium-ion technology is at the heart of it all. However, achieving these feats is no small task. It requires relentless research and innovation, particularly in the selection and optimization of materials, including the metals used in the anode and cathode components of the lithium-ion cell.
The quest for the perfect combination of materials and chemical compounds is driven by the need to enhance performance, extend lifespan, and reduce costs. Scientists and engineers are constantly exploring new materials, metal alloys, and combinations, such as silicon anodes or solid-state electrolytes, that can push the boundaries of what lithium-ion batteries can do. From experimenting with various lithium compounds and metal oxides to investigating alternative materials like lithium-sulfur (Li-S) or lithium-air (Li-O₂) batteries that could offer better efficiency or sustainability, the research is as diverse as it is important. This ongoing effort to refine and improve lithium-ion battery technology, with a focus on the role of metals and their chemical forms, is crucial for meeting the growing demands of both consumers and industries, ensuring that these batteries remain at the cutting edge of energy storage solutions
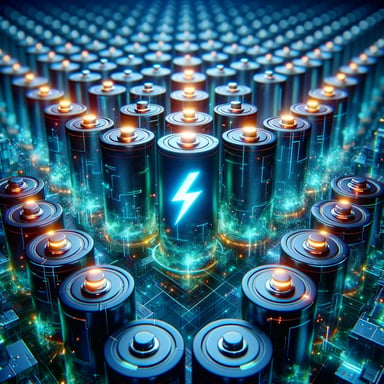
Lithium-ion batteries are used in different technologies such as the Hybrid Electric Vehicles , which use both battery as well as electric motor engines to increase the fuel efficiency . A battery is essentially many electrochemical cells connected in series or parallel to provide voltage and capacity. Each cell contains a positive (cathode) and negative (anode) electrode divided by an electrolytic solution, simply called as an electrolyte, with dissociated salt that allows ion transfer between electrodes. When these electrodes are connected to an external source, electrons are released as a result of chemical reaction and therefore for current to be tapped . The electrical energy that a battery is able to give is a function of both the cell and its capacity which are dependent on the chemistry of the battery. For the purpose of application, Nickel Metal Hydride (Ni-MH) is the common battery technology currently being used.
CATHODE MATERIALS The cathode material in Li-ion battery chemistry is the major and active source of all the Li-ions. The preference of positive electrode materials depends on rechargeable Limetal or Li-ion batteries. The Li-metal, when used in rechargeable Li batteries, the metal acts as a negative electrode, therefore the positive electrode does not need to be lithiated. In the case of Li-ion, because carbon electrode which acting as the negative doesn’t have Li, the positive terminal must act as source of Li; therefore intercalation compound is required for the cell assembly.
ANODE MATERIALS Currently, the two most commonly used anode materials are those based on carbon (graphite) and lithium alloyed metals. One of the commercialized lithium alloyed metal is the oxide spinel the structure. To avoid issues in the cycling and safety which are associated with dendrite formation on lithium anodes, it is advisable to use the minimal potential intercalation electrode. The element found in the graphite intercalation alloy protects the inserted lithium, making it less reactive towards electrolytes. This will make the amount of Lithium in the lithiated material less, which comes with both advantage and disadvantage. The advantage is that it accounts for any safety concerns regarding the flammability of the electrochemical reactions.
The kilns that are predominantly used in battery production are.
A cornerstone in the realm of advanced battery production, represents the pinnacle of efficiency and uniformity. This type of kiln, known for its continuous operation, is designed to handle a multitude of products, offering unparalleled flexibility in processing. The Roller Hearth Kiln operates by transporting materials through the kiln on rollers, which ensures consistent heating and cooling rates — critical factors in the manufacture of high-quality battery components. Its adaptability to various atmospheres and temperature profiles makes it an indispensable tool for manufacturers aiming to meet the rigorous demands of today's battery market. Whether you're processing cathodes, anodes, or other ceramic components, the Roller Hearth Kiln stands out for its ability to achieve precise temperature control and rapid processing speeds, thereby enhancing both product quality and manufacturing efficiency.
Next in line for cutting-edge battery production is the Pusher Kiln, a stalwart in the industry known for its robust performance and exceptional reliability. This kiln type excels in the mass production of battery materials, utilizing a mechanism that methodically pushes trays of product through the heating chamber. The Pusher Kiln is celebrated for its ability to maintain uniform temperatures across a wide range of settings, making it an ideal choice for the intricate processes involved in battery component manufacturing. Its design allows for precise control over the atmosphere within the kiln, a critical factor when aiming to achieve specific material properties in the final product. The efficiency of the Pusher Kiln lies in its continuous push mechanism, which ensures a steady flow of products through the kiln, optimizing production rates and minimizing downtime. For manufacturers focused on scalability and consistency, the Pusher Kiln offers a solution that is both time-tested and pioneering, embodying the perfect blend of tradition and innovation in battery manufacturing technology.
Rotary Kiln
Emerging as a formidable player in battery production technology, the Rotary Kiln is a marvel of engineering designed to meet the complex demands of modern battery component manufacturing. This versatile kiln rotates the material, allowing for an even heat distribution that is essential for the thermal treatment of battery materials. The Rotary Kiln's ability to operate under a wide range of temperatures and atmospheric conditions makes it a highly adaptable option for manufacturers looking to optimize their production processes. Its rotating drum ensures that materials undergo consistent heating and cooling cycles, a factor vital for achieving the high precision required in battery component quality. The design of the Rotary Kiln allows for excellent heat transfer and temperature control, making it particularly suitable for the synthesis and processing of advanced materials used in battery production. With its capacity for customization in terms of length, diameter, and rotation speed, the Rotary Kiln offers a scalable solution that can be tailored to the specific needs of battery manufacturers, ensuring both efficiency and effectiveness in the production line. Integrating seamlessly into the battery manufacturing ecosystem, the Rotary Kiln stands as a testament to innovation and quality, driving forward the standards of excellence in battery technology.
Therser UK will design and build and install all the above, offering a full turnkey solution.
Positioned right after the kiln outlet, a conveyor serves as an integral extension of the cooling zone, seamlessly integrating with the Saggar Handling System (SHS).
The SHS can do
Filling and weighing to the desired amount involves a meticulously calibrated process, ensuring each saggar is filled with the exact quantity of material needed. Our cutting-edge technology guarantees precision in every step, eliminating guesswork and reducing waste. By automating the process, we ensure consistency in product quality, optimizing the efficiency of your operations. This critical stage in the Saggar Handling System is designed with flexibility in mind, allowing adjustments to meet the specific requirements of your product, thereby ensuring that every saggar is prepared with the utmost accuracy and care.
Stacking the saggars is executed with meticulous precision and care, incorporating advanced robotic systems designed to handle each saggar with the utmost delicacy. This phase in the Saggar Handling System utilizes sophisticated algorithms to determine the optimal stacking pattern, ensuring stability and maximizing space efficiency within the kiln. Our technology enables precise placement and alignment, reducing the risk of damage during the firing process. The automated stacking process not only enhances the throughput by significantly reducing manual labor but also ensures a consistent and uniform product quality by maintaining the ideal conditions for each saggar. With the ability to adjust the stacking configuration based on the specific requirements of your products, our system offers unparalleled flexibility and efficiency, making it a vital component of the Saggar Handling System.
Detecting and intercepting cracked saggars with unparalleled precision, our Saggar Handling System employs state-of-the-art sensors designed to identify even the slightest imperfections. This preemptive approach ensures that any potential issues are addressed before they can escalate, safeguarding the integrity of your product and the efficiency of the firing process. The sensors meticulously scan each saggar for cracks that could compromise the quality of the firing, triggering an immediate response to remove any faulty units from the production line. This critical feature not only prevents the risk of contaminating your product but also minimizes the possibility of equipment damage, thereby maintaining optimal operational flow and reducing costly downtimes. By integrating this advanced detection technology, our system provides an added layer of quality control, ensuring that only saggars in perfect condition proceed through the handling and firing processes, ultimately enhancing the overall reliability and effectiveness of your operations.
The recovery machine innovatively redefines the process of collecting residual powder material, offering a seamless and efficient solution. By ingeniously overturning the saggar into meticulously designed closed containers, this phase of the Saggar Handling System ensures that every particle of valuable powder material is captured without spillage or loss. This not only maximizes resource utilization but also significantly reduces the environmental impact by minimizing dust and waste. The closed container design ensures that the collected material remains uncontaminated and ready for reuse or recycling, aligning with sustainability goals and reducing operational costs. This thoughtful integration of the recovery machine into the SHS demonstrates our commitment to creating systems that are not only productive and fuel-efficient but also environmentally responsible, ensuring that your operations contribute positively to both your bottom line and the planet.
Cleaning and inspecting each saggar ensures it is impeccably prepared for reloading with product. Leveraging advanced cleaning technologies, our system thoroughly removes any residues or particulates from previous cycles, guaranteeing a pristine environment for your products. This is followed by a comprehensive inspection process, where cutting-edge vision systems and precision sensors scrutinize every inch of the saggar for any signs of wear, damage, or contamination. This ensures that only the saggars meeting the highest standards are reloaded, maintaining the integrity and quality of your firing process. This crucial step not only enhances the longevity and reusability of the saggars but also reinforces the consistency and excellence of your final product. By integrating these meticulous cleaning and inspection protocols, our Saggar Handling System elevates the operational efficiency and product quality to new heights, ensuring your operations are ready to meet the demands of production with unmatched precision and care.
The configuration of your SHS will be led by you. We will aid in the design to make it productive and fuel efficient.
A saggar is a deep ceramic box used in industrial applications to hold materials or items while they’re being fired.
The production of battery material requires the use of complex multi-metal oxide active powders. These powders are made by reacting the raw ingredients together at high temperatures, at which point the material becomes incredibly corrosive during this calcination process.
saggars can be used to contain powders, granules, and small components,
they can be used as enclosures, helping to retain the vapours of volatile ingredients as they are processed at high temperatures. Saggars can protect objects from contamination.
Therser are the UK’s largest Kiln and Furnace manufacturing company, we are also the only UK company that can offer RHK’s (Roller Hearth Kilns) and SHS’s (Saggar Handling Systems) for various industries and market sectors, including the manufacture of CAM (Cathode Active Materials) for the Lithium-Ion Battery sector which we are currently engaged in with some of our customers.
Therser UK is an established Kiln engineering specialist based in the UK and as such can provide full maintenance and servicing any other type of heat treating equipment that your company may use.
Therser UK has a wealth of experience in the following areas:
- Therser UK offers turnkey solutions, ensuring a seamless and complete package from concept to commissioning.
- By working in partnership with you, Therser UK tailors its approach to meet your unique needs and project goals.
- Each kiln is made to your specification, reflecting our commitment to customizing our products for optimal performance.
- Therser UK incorporates all up-to-date technology in our kilns to maximize efficiency and sustainability.
- We offer product test fires for a variety of industries including Battery Material, Aerospace, Automotive, and Metals, demonstrating our versatility and expertise.
- Therser UK provides Computational Fluid Dynamics (CFD) data, supporting the optimization and safety of our kiln designs.
- Our in-house 3D modelling capabilities enable precise visualization and engineering of your project before construction begins.
- From initial design concepts to final realization, Therser UK ensures your vision is accurately brought to life.
- Every project is expertly managed to adhere to timelines, budgets, and quality standards.
- High-grade materials are used or chosen by you to guarantee the durability and performance of our kilns.
- Therser UK's in-house panel building ensures that all control systems meet our high-quality standards.
- Experience a virtual reality tour of your project, offering a unique preview of the final product.
- Our fully bespoke automation systems are tailored to enhance efficiency and precision in operations.
- We provide refractory solutions to enhance the longevity and performance of our kilns under high temperatures.
- Therser UK ensures full compliance with all country-specific regulations, guaranteeing global operational excellence.
- Every kiln undergoes rigorous quality checks to uphold Therser UK's high standards of excellence.
- We pride ourselves on shipping all over the world, reflecting our global reach and reliability.
- Delivering on time is a cornerstone of our service, ensuring that project timelines are respected and met.
- As industry leaders, Therser UK sets standards in kiln design, innovation, and customer service.
- Our engineering team provides remote support, ensuring expert assistance is just a call away.
- Machinery onsite training by Therser UK equips your team with the knowledge and skills for optimal kiln operation.
- We offer kiln servicing contracts to maintain peak performance and minimize downtime.
- Therser UK supplies kiln spare parts, ensuring your operations run smoothly with immediate access to essential components.
Therser UK’s world of innovative kiln solutions and thermal engineering excellence, it's clear that their success is not just in the technology they use but in their approach to partnership with clients. Therser UK’s commitment to providing turnkey solutions, tailored to the unique specifications and needs of their clients, ensures that every project is a testament to precision, quality, and innovation. From offering state-of-the-art technological integrations to ensuring compliance with global standards, Therser UK sets the bar high for what is possible in the industry. Our dedication to delivering on time, utilizing high-grade materials, and providing unmatched support and training demonstrates a holistic approach to customer satisfaction and project success. Whether it's through remote engineering support, onsite training, or innovative refractory solutions, Therser UK is not just a supplier but a partner in the truest sense. As we look to the future, Therser UK’s trajectory is set to redefine industry standards, continually pushing the boundaries of innovation, efficiency, and customer-centric solutions in the world of kiln manufacturing and thermal solutions.
BATTERY MATERIALS
TALK TO US TODAY
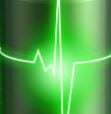
