Heat Treatment Processes

Sintering

Sintering is the process of compacting and forming a solid mass of material by pressure or heat without melting it to the point of liquefaction.

Sintering happens as part of a manufacturing process used with metal and ceramic and other materials. The atoms in the materials diffuse across the boundaries of the particles, fusing the particles together and creating one solid piece. Because the sintering temperature does not have to reach the melting point of the material, sintering is often chosen as the shaping process for materials with extremely high melting points. Sintering can be observed when ice cubes in a glass of water adhere to each other, which is driven by the temperature difference between the water and the ice.

Sintering is frequently considered successful when the process reduces porosity and enhances properties such as strength. In some special cases, sintering is precisely applied to enhance the strength of a material while conserving porosity, like in filters or catalysts, where gas absorbency is a priority. During the firing process, atomic diffusion drives powder surface elimination in different stages, starting at the formation of necks between powders to final elimination of small pores at the end of the process.

Sintering is part of the firing process used in the manufacture of crockery and other ceramic objects. These objects are made from substances such as glass. Some ceramic raw materials have a lower absorption for water and a lower plastic index than clay requiring organic additives in the stages before sintering.

Generally, most, if not all metals can be sintered. This applies especially to pure metals produced in vacuum which suffer no surface contamination. Sintering under atmospheric pressure requires the use of a protective gas. Sintering, with subsequent reworking, can produce a great range of material properties. Changes in density alloying and heat treatments can alter the physical characteristics of various products.

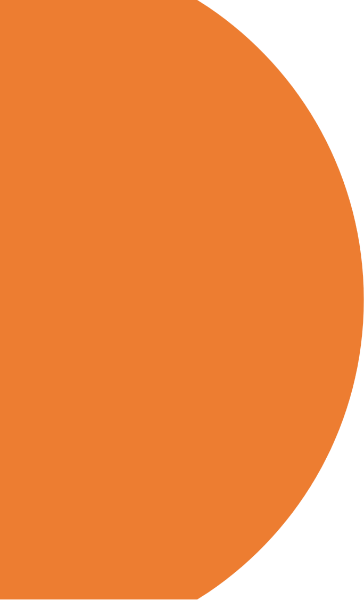
Calcination
Calcination refers to thermal treatment of a solid chemical compound, mixed carbonate ores, whereby the compound is raised to high temperature without melting under restricted supply of ambient oxygen generally for the purpose of removing impurities or dangerous substances. Calcination is carried out in furnaces or kilns, various designs including shaft furnaces, rotary, hearth kilns.
Carbonization
Carbonization is the conversion of organic matters like plants and dead animal remains into carbon. The carbonization of wood in an industrial setting usually needs a temperature above 280 °C, which gives up energy and hence this reaction is said to be exothermic. This carbonization, which can also be seen as a spontaneous breakdown of the wood, continues until only the carbonised residue called charcoal remains.
The gas produced by carbonization has a high content of carbon monoxide which is poisonous when breathed. Therefore, when working around the kiln or pit during operation and when the kiln is opened for unloading, care must be taken to allow the carbon monoxide to be dispersed.
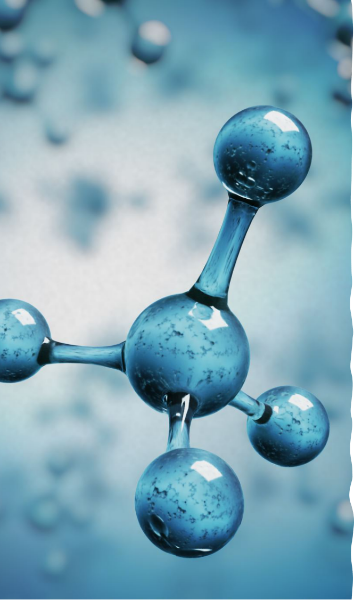
Oxidation/Reduction
- Oxidation is the loss of electrons or an increase in the oxidation state, while reduction is the gain of electrons or a decrease in the oxidation state.
- In redox processes, the reductant gives electrons to the oxidant. Therefore, in the reaction, the reductant or reducing agent loses electrons and is oxidized, and the oxidant or oxidizing agent gains electrons and is reduced. The pair of an oxidizing and reducing agent that is involved in a particular reaction is called a redox pair. The oxidation itself and the reduction alone are each called a half reaction because two half-reactions always occur together to form a whole reaction.
- Oxidation firstly inferred to a reaction with oxygen to form an oxide. Later, the term was expanded to encompass oxygen-like substances that accomplished parallel chemical reactions. Ultimately, the meaning was generalized to include all processes involving the loss of electrons.
- Substances that have the ability to reduce other substances (cause them to gain electrons) are said to be reductive or reducing and are known as, reductants, or reducers. The reductant (reducing agent) transfers electrons to another substance and is itself oxidized. And, because it donates electrons, the reducing agent is also called an electron donor. Firstly, the word reduction originally referred to the loss in weight upon heating a metallic ore such as a metal oxide to extract the metal. In other words, ore was "reduced" to metal.
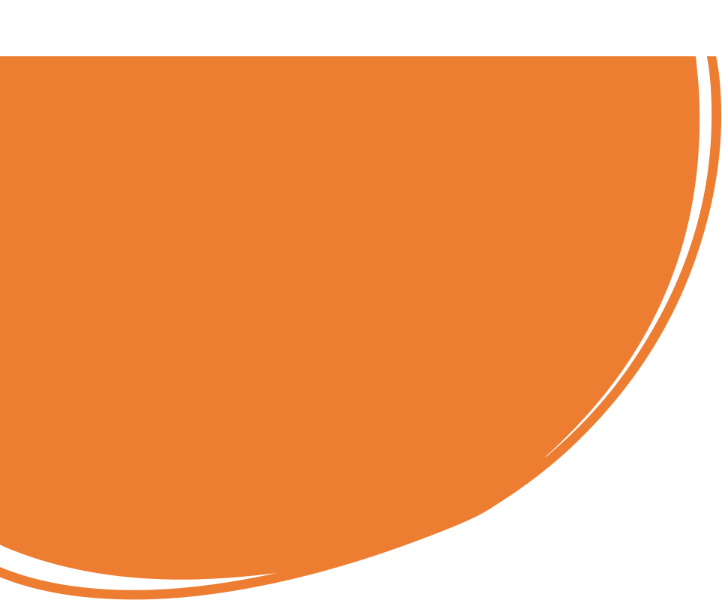
- Tempering is a process of heat treating, which is used to increase the strength of iron-based alloys. Tempering is usually performed after hardening, to reduce some of the excess hardness. The exact temperature determines the amount of hardness removed and depends on both the specific composition of the alloy.
- Tempering is most often performed on steel that has been heated above its upper critical temperature and then quickly cooled, in a process called quenching, using practises such as immersing the hot steel in water, oil, or compressed air. The quenched steel, being placed in or very near its hardest possible state, is then tempered to incrementally decrease the hardness to a point more suitable for its application.
Debinding
The debinding process removes the primary binding material from the moulded component. Generally, there are many ways to the debinding process, and the object goes through more than one cycle to ensure as much of the binding material is taken off as possible before sintering. After the debinding step the part is semi-porous, which allows the secondary binder to easily escape during sintering cycle. Why debinding is needed, without this critical step the part would not be as sturdy. Debinding also prevents furnaces from clogging which can lead to added expenses on the production side. It also is a faster process to debind and then to sinter, versus just sintering alone Thermal debinding is a method within a temperature-controlled environment. It has cost effective equipment and has a long processing cycle.
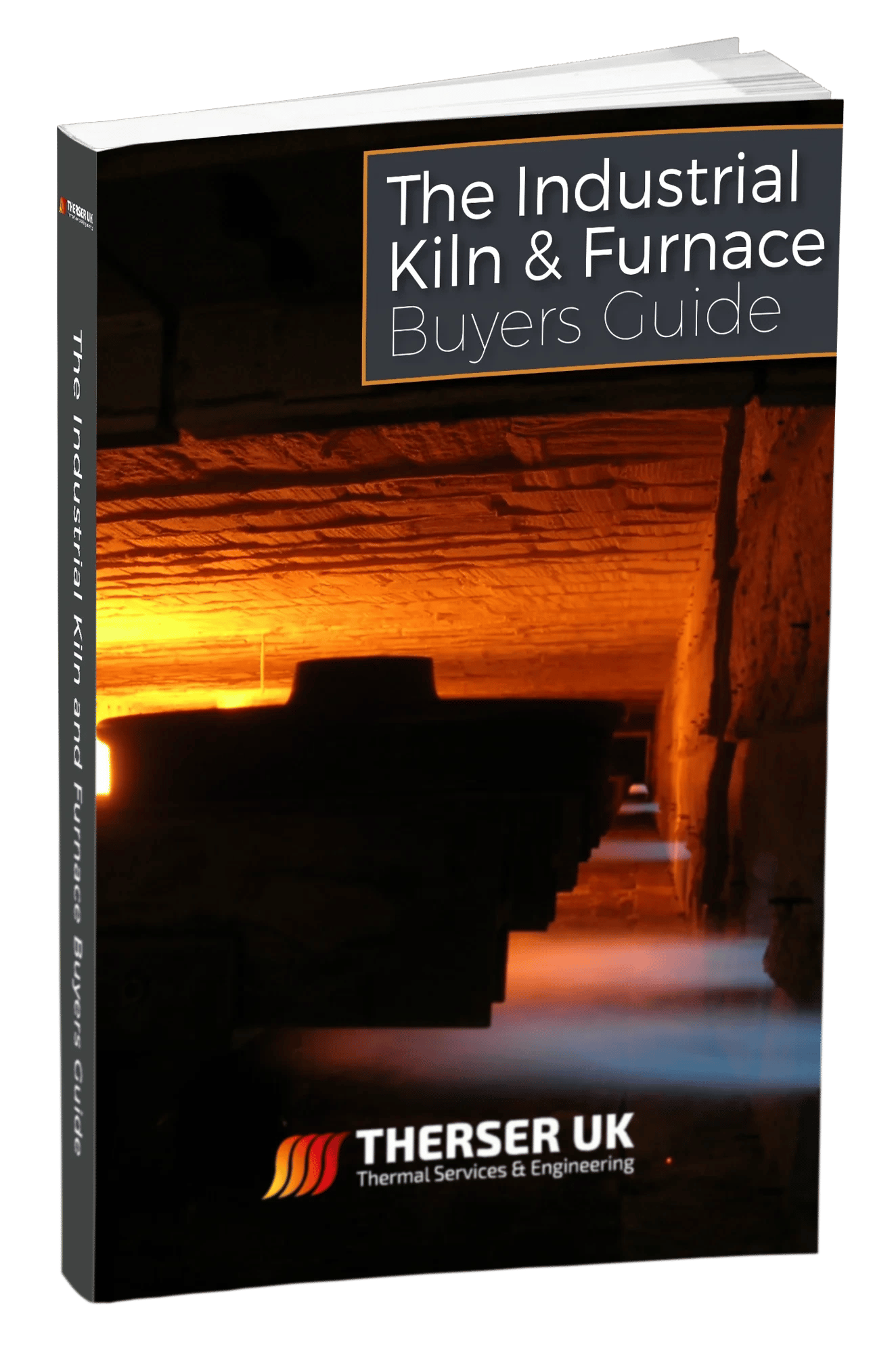
DOWNLOAD THE INDUSTRIAL KILN & FURNACE BUYERS GUIDE
If you need, or may need in the future, to invest in an industrial kiln, furnace or oven, then get a copy of this FREE guide today.
Discover:
- How to choose the right type of kiln or furnace
- How to avoid the most common mistakes with industrial kilns and furnaces
- How to ensure maximum fuel efficiency
So confirm your correct email address using the form provided and your copy will be in your inbox within seconds!
OUR CERTIFICATIONS
REVIEWS
TALK TO US TODAY
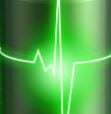
